铝和镁零件是许多行业中使用最广泛的两种原型金属。今天,大多数汽车公司使用原型压铸来进行设计验证,有时在开始生产之前进行生产验证。压铸的原型应用不需要长寿命、短周期、高产出率和较低的零件成本,而生产型压铸工具/模具就是为这些而设计的。因此,原型压铸工具由较便宜的钢材(如P20)制成,并且在许多情况下重新使用现有的模架以减少时间和成本。这种技术允许使用与大批量生产完全相同的材料进行零件的原型开发,而无需在昂贵和复杂的生产工具上进行初始投资。
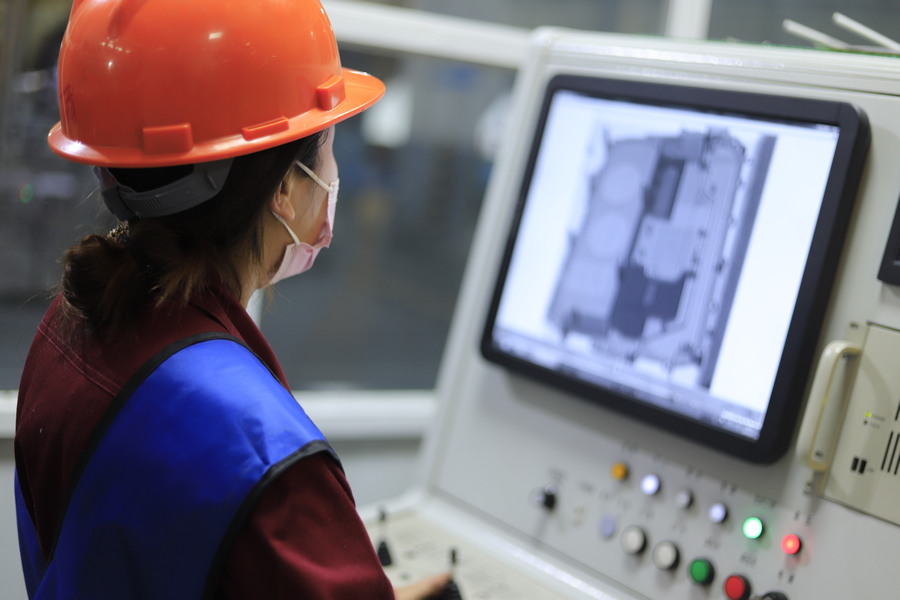
铝和镁零件是许多行业中最广泛使用的两种原型金属。今天,大多数汽车公司使用原型压铸来做设计验证,有时在启动生产之前进行生产验证。
压铸的原型应用不需要长寿命、短周期、高产出率和较低的零件成本,而生产型压铸工具/模具就是为这些而设计的。因此,原型压铸工具由较便宜的钢材(如P20)制成,并且在许多情况下重新使用现有的模架以减少时间和成本。这种技术允许使用与大批量生产完全相同的材料进行零件的原型开发,而无需在昂贵和复杂的生产工具上进行初始投资。
其他策略,如使用单腔模具,使用可互换或可交换的工具刀片的模块化工具设计,以及用预硬钢和非氮化钢制造刀片,大大减少了制造时间和成本。冷却系统也可以进行优化,以降低成本,因为循环时间不需要像大批量生产时那样快。与生产型压铸相比,原型工具可以在4至6周内快速制成,这取决于最终零件的几何形状。
在使用铝压铸原型时,进行设计变更也相对容易。由于模具嵌件可以互换,而且是用廉价的钢材制造的,因此可以快速实施设计变更。同样,在特征上略有不同的零件系列可以用镶件来制造,避免了昂贵的多种工具。这样就可以在全面生产之前快速验证设计方案,创造出与最终产品非常相似的零件。